Drinking water sampling occurs at intakes, reservoirs and in the reticulation network to ensure compliance with national guidelines.
Water Service
Douglas Shire Council is a registered water service provider, SPID 558, providing drinking water services to about 15,000 customers.
Council is operating under an approved Drinking Water Quality Management Plan (DWQMP) to ensure consistent supply of safe drinking water in order to protect public health and as required under the Water Supply (Safety and Reliability) Act 2008.
More information is available in the Drinking Water Service Annual Report.
Douglas Drinking Water Service Annual Report
The Douglas Drinking Water Service Annual Report 2024 documents the performance of Douglas Shire Council as a Drinking Water Service Provider (SPID 558) during the financial year 2023 – 2024.
The report provides a mechanism to report publicly on the performance in managing drinking water services and drinking water quality.
Water Treatment Overview
Mossman, Whyanbeel and Daintree Water Treatment Plants treat water from Rex Creek, Little Falls Creek and Intake Creek and/or Daintree Bore respectively. All treatment plants have the following process steps:
- Prefiltration
- Ultrafiltration
- Chlorination
- The Whyanbeel WTP has a sodium carbonate pH adjustment step.
Read more about the detailed water treatment process below
Prefiltration
Raw water is filtered through prefilters that remove initial coarse material, such as sand and grit. The prefilters provide a duty/standby operation. The prefilters are cleaned by automated back-washing using raw water.
During heavy rainfall events when raw water turbidity is high, water is additionally passed through a hydrocyclone to separate and remove heavier particles such as sand and gravel. During normal operations, the hydrocyclone is bypassed.
Ultrafiltration
The water treatment plants utilise ultrafiltration membranes for filtration. These membranes are often referred to as UF Cartridges. The semipermeable UF membranes have the ability to physically reduce organic material, protozoan, bacteria and viruses present in water.
Operating, monitoring and alarm functions of the ultrafiltration treatment are managed via an online process.
The cleaning of the UF Cartridges is via an automated backwashing sequence.
Backwash Recovery
At Mossman Water Treatment Plant, prefilter and ultrafiltration water only backwashes are recycled through the backwash recovery plant and fed back into the head of works to recover water. This process helps reduce water extraction volumes from Rex Creek intake.
By utilising the backwash recovery plant, approximately 1 ML of water gets recovered daily.
Chlorination
Together with ultrafiltration, disinfection with chlorine provides a second barrier towards pathogens. After dosage at the water treatment plants, a low concentration of chlorine remains in the water distribution system, ensuring that the water is safe for consumption. Chlorine disinfection kills bacterial pathogens and greatly reduces the numbers of viral and protozoan pathogens.
Water Quality Monitoring
Drinking water sampling occurs at intakes, reservoirs and in the reticulation network to ensure compliance with the Australian Drinking Water Guidelines (ADWG).
Water quality verification monitoring includes regular testing of individual reticulation zones with monthly sampling at the reservoirs.
Supporting programs for the verification of drinking water quality include;
- Water treatment plants and reservoirs that have SCADA alarms for action and critical limits and are operated under critical control points.
- Reservoir inspections that are done regularly to ensure that the reservoirs are intact and that any points of ingress are repaired.
- Network operations that have a flushing program that ensures the chlorine residual is above 0.2 mg/L.
If you rely on a consistent water supply for medical reasons, please join our Vulnerable Persons Register so we can work with you in the unlikely event any issues arise.
Water Flushing
Flushing is a process used for cleaning or “scouring” the interior of water distribution mains (pipes) by sending a rapid flow of water through the mains. Distribution mains deliver water to homes, businesses and hydrants in your locality. Most importantly, flushing helps maintain water quality.
Flushing is used to maintain chlorine levels at the right volume for disinfection purposes. Chlorine dosing is a common disinfection practice in water treatment, and it ensures that bacteria are not thriving in the water or pipe network.
Chlorine naturally degrades the longer it is in water, which means that water sitting in pipes for long periods of time or further out from the treatment plant can have concentrations lower than the required levels, creating a potential health risk.
Lines are flushed to keep water moving, drawing fresher chlorinated water through and keeping pipes from stagnating, thus preventing any risks. If water does become stagnant in pipes, or water quality becomes impacted (by sediment, rust, or other contaminants that can sometimes enter into a water system from broken pipes), it is essential that regular flushing occurs.
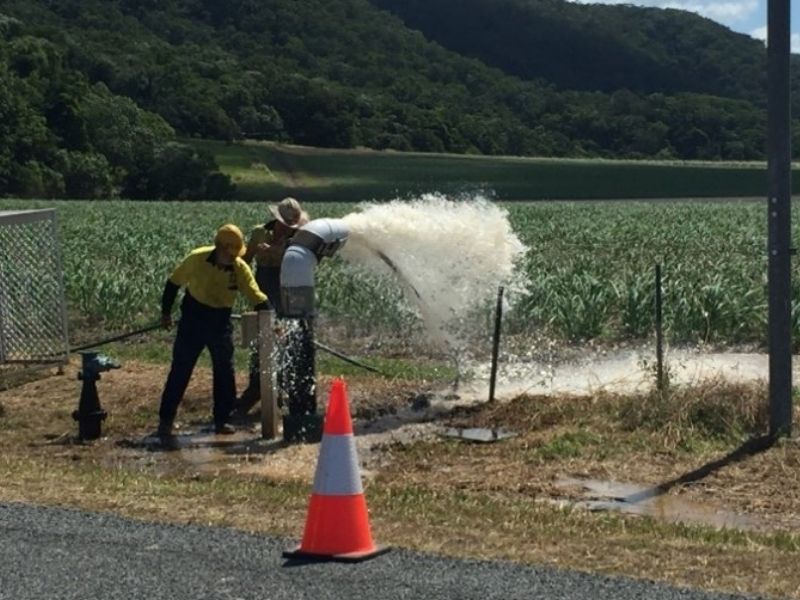
What a waste of good clean water!
You have probably seen it many times and thought to yourself, “what a waste of good clean water!” Flushing can be frustrating to residents in places with low water supplies or those who pay high premiums to keep their taps flowing. While it may seem like a waste of treated water, flushing of water lines is essential to keeping your water safe and maintaining the integrity of a pipe network. If you see a hydrant running, it isn’t the Water Team just wasting water. The team is actually working hard to make sure you have safe drinking water. So, no matter how you feel about it, you shouldn’t attempt to turn off the hydrant at any time as this may cause more issues with the water quality and could affect public health.
Why not collect the wasted water to be reused elsewhere?
If the water could be kept and reused, it would be. While it would be an ideal outcome to transport the wasted water to a park or put it to good use elsewhere, it is currently too costly to implement, and diverting the excess is the only viable solution. In the meantime, there are various initiatives being explored for diverting the flushed water to garden beds in the different locations where flushing occurs. There are some garden irrigation systems currently operating in Daintree Township to ‘flush’ at set times to draw water through to assist in water quality at the end of water lines. Other locations are also being reviewed to maximise the use of the flushed water, and where practical, will be rolled out as and when budget is allocated.
What should I do if I see water flushing?
The answer is simple: Do nothing. Please do not touch any water infrastructure, even if you think there is a problem, as you may create a bigger problem in doing so. If you are concerned that there is a major issue, such as a large water main break, please contact staff on 07 4099 9444 to report what you see.
Educational Posters
Wet Tropics Report Card
Wet Tropics Waterways was launched in July 2016 with the release of the ‘Pilot Report Card’ in December 2016 which reported on the 2014-15 year.
The purpose of this document is to provide detailed information on the methods used to produce assessments of condition and state for the freshwater, estuarine, inshore marine and offshore marine environments.
Specifically, this document describes the following.
- The data collection methods
- The scoring methods
- The confidence rating method
An overall condition grade was provided for each reporting zone within each environment (basin, estuary, inshore marine and offshore marine).